Ephemeral Inks: The Science and History of Typewriter Ribbons
The clatter of keys, the rhythmic ding of the carriage return – these are sounds instantly recognizable as the voice of the typewriter. But behind the satisfying mechanics, there's a often-overlooked element crucial to the process: the ribbon. More than just a strip of fabric, typewriter ribbons represent a fascinating intersection of chemistry, engineering, and artistry. They are the ephemeral inks of a bygone era, each one bearing witness to countless stories, documents, and creative endeavors. It's a history inextricably linked to the evolution of office equipment, vintage technology, and the passionate world of collectible typewriters.
My grandfather, a meticulous accountant, kept a cabinet overflowing with ribbons. Not just the standard black, but vibrant reds, blues, and even a faded purple. He’s gone now, but the scent of those old ribbons – a peculiar mix of ink, solvent, and aged fabric – remains a powerful trigger for memories of his quiet dedication, his precise work, and the comforting rhythm of his Remington. He treated those ribbons with a reverence most would find odd, carefully storing them in labeled tins, almost as if they were precious gems. That early exposure instilled in me an appreciation not just for typewriters, but for the often-ignored details that give them character.
The Early Days: Fabric and Pigment
The earliest typewriters, dating back to the mid-19th century, used remarkably simple ribbons. Initially, these were made of plain, woven cotton, sometimes treated with a stiffening agent. The ink itself was a mixture of pigment – often lampblack or ochre – suspended in a drying oil, like linseed oil. Applying this ink to the fabric was a laborious process, frequently done by hand, and the resulting ribbons were far from perfect. The image they produced would often be uneven, prone to fading, and the early ribbons wore out quickly. The technology felt nascent, an experimental whisper of what was to come.
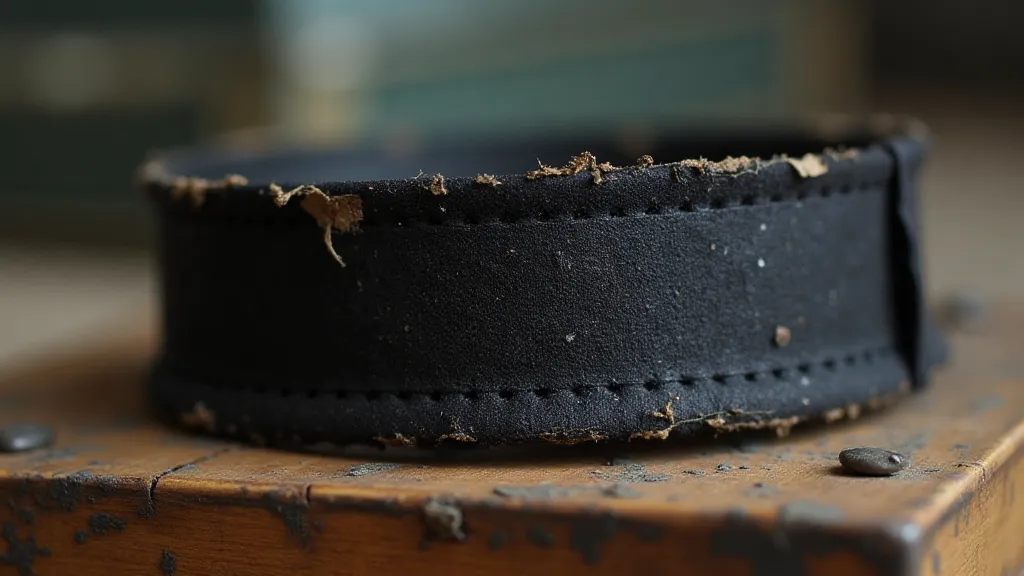
The Rise of Silk and the Improvement of Ink
The transition to silk ribbons marked a significant improvement. Silk’s smoother surface provided a more consistent printing surface, and the finer weave allowed for sharper impressions. However, the ink remained the biggest hurdle. The oil-based inks were prone to smudging and were susceptible to deterioration over time. The late 19th and early 20th centuries saw a flurry of experimentation with different ink formulations. Manufacturers began incorporating dyes, which offered richer and more vibrant colors compared to the more muted pigments. These early dyes, however, were often unstable and prone to fading or bleeding.
This era was also characterized by the rise of large-scale ribbon manufacturing. Companies like Smith Corona and IBM realized the potential of controlling this vital component of their typewriters, ensuring a steady supply of high-quality ribbons tailored to their specific machines. This shift from small-scale artisanal production to industrialized manufacturing brought down the cost of ribbons, making them more accessible to a wider audience.
The Dye Revolution and the Rise of Synthetic Fabrics
The true revolution arrived with the development of synthetic dyes. These dyes, often derived from coal tar, offered unparalleled stability and a far wider spectrum of colors. Suddenly, ribbons weren't limited to black, red, and a few muddy browns. Emerald greens, sapphire blues, and even vibrant oranges became available, adding a touch of personality and flair to correspondence and documents. The early 1930s also saw the introduction of nylon ribbons, which were stronger, more durable, and more resistant to wear than their silk or cotton predecessors. The printing quality significantly improved thanks to the more uniform and less absorbent material.
The science behind dye formulation was complex and involved understanding the chemical interaction between the dye molecule, the fabric, and the typewriter’s printing mechanism. Manufacturers employed teams of chemists and engineers dedicated to perfecting these processes, striving for the ideal balance of color intensity, durability, and printability.
My own collection includes a few exceptionally rare ribbons – a dusty rose pink ribbon believed to have been used by a theatrical company, and a vibrant teal ribbon attributed to a women’s suffrage organization. These aren't just pieces of fabric; they're fragments of history, each whisper of color hinting at a story waiting to be unearthed.
The Science of Color and Printing
The printing process itself relies on a clever interplay of physical and chemical principles. The ribbon sits between the inked typebars and the paper. As the typebar strikes, it presses the ribbon against the paper, transferring a microscopic layer of ink. The quality of this transfer depends on several factors: the ink's viscosity, the ribbon’s tension, the paper’s absorbency, and the typewriter’s alignment.
Different dyes absorb and reflect light differently, determining the perceived color. The intensity of the color depends on the concentration of the dye and the efficiency of the transfer process. The subtle variations in shade and tone that characterize vintage typewriter prints are often a result of imperfections in the ribbon or the printing mechanism – imperfections that, to some collectors, add to the charm and authenticity of the document.
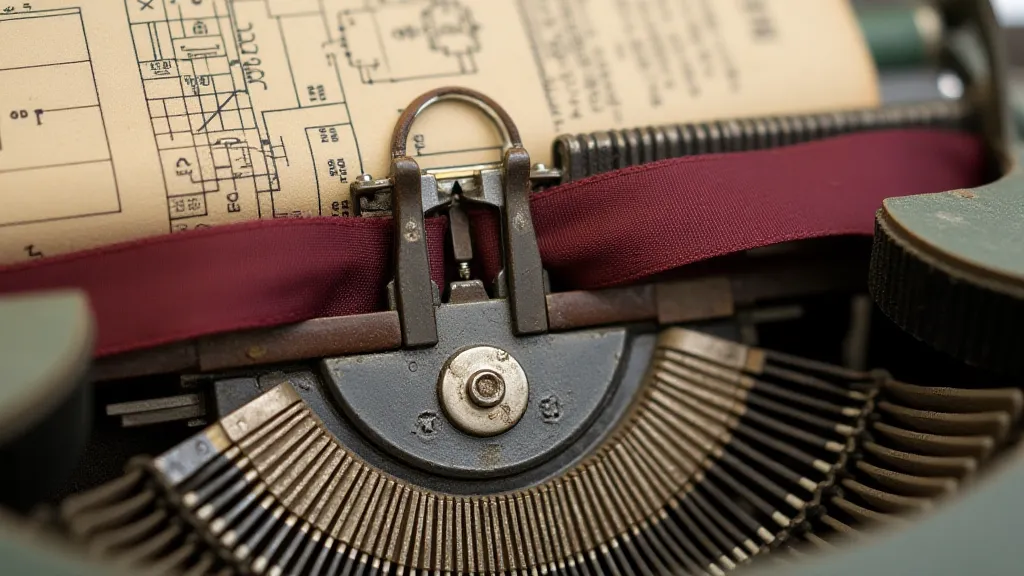
The Decline and the Legacy
The rise of personal computers and word processors marked the beginning of the typewriter ribbon's decline. While digital printing offers unparalleled convenience and flexibility, it lacks the tactile and visual qualities that make typewriter printing so appealing. Today, typewriter ribbons are primarily used by collectors, enthusiasts, and artists who appreciate the unique aesthetic and the nostalgic charm of this vintage technology.
Restoring antique typewriters often involves sourcing and replacing ribbons. Finding original ribbons can be challenging, and reproductions are often of varying quality. The scent, the subtle variations in ink density, the slight imperfections – these are all part of the experience. These attributes are subtle indicators of authenticity and add significantly to the typewriter's character.
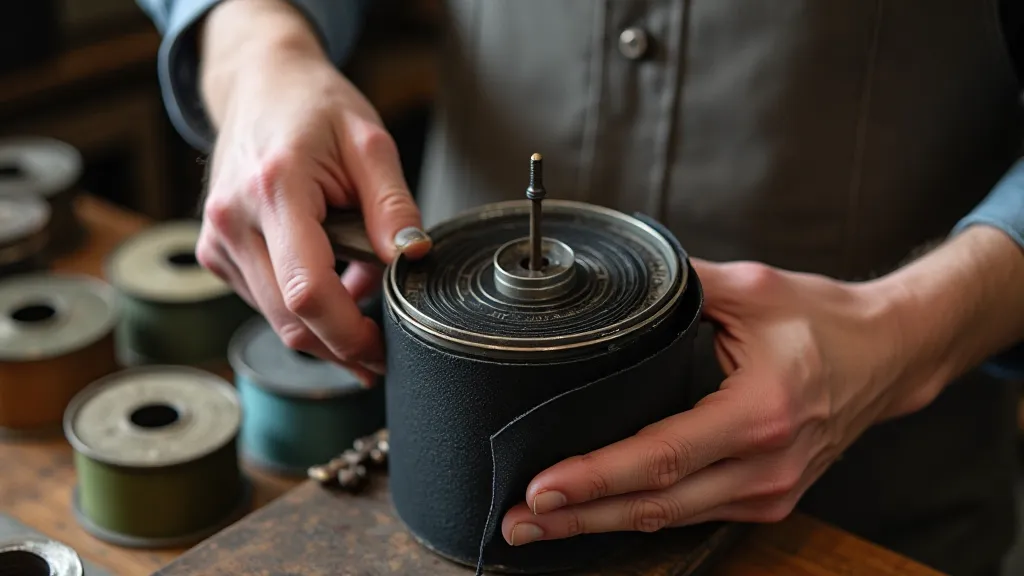
More Than Just Ink
The history of typewriter ribbons is a fascinating microcosm of technological innovation and social change. It’s a story of chemists striving for the perfect shade of blue, of engineers optimizing printing processes, and of countless individuals using these ribbons to record their thoughts, their dreams, and their stories. These ephemeral inks represent more than just a printing medium; they are tangible links to a bygone era, reminders of a time when technology was simpler, more deliberate, and imbued with a sense of craftsmanship. They are a testament to the enduring power of analog technology and the beauty of imperfection. They remain, even now, profoundly evocative.